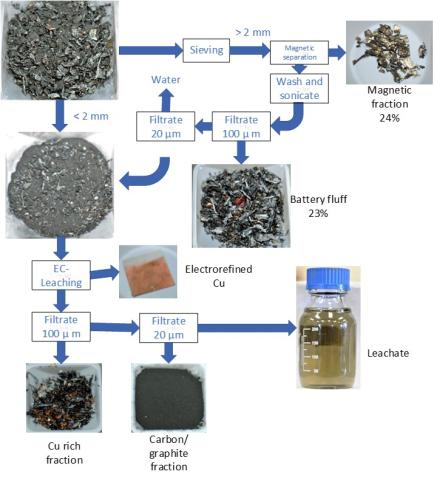
This CMI-funded research is part of a project based at Idaho National Laboratory with input and supplies from CMI Team Members Retriev Technologies and Solvay, and supplies from American Zinc Recycling.
Achievement:
Demonstrate the flexibility of the electrochemical leaching process, to different feedstocks. High Ni content shredded battery feedstock was obtained from American Zinc Recycling (AZR). High leaching efficiencies of 97.82% and 99.66% where achieved for cobalt and lithium, respectively.
A comprehensive co-recovery process, with different value streams, such as graphite, copper, and steel scrap was developed
Significance and Impact:
- Cobalt, lithium and graphite can be recovered from shredded lithium ion batteries with low pre-processing requirements
- Can recover several revenue streams (steel, copper, graphite and critical material)
- Electrochemical leaching process is flexible to different battery chemistries, including those with low cobalt content
Details and Next Steps:
Investigate how the downstream separation flowsheet can be modified for high nickel content leachate
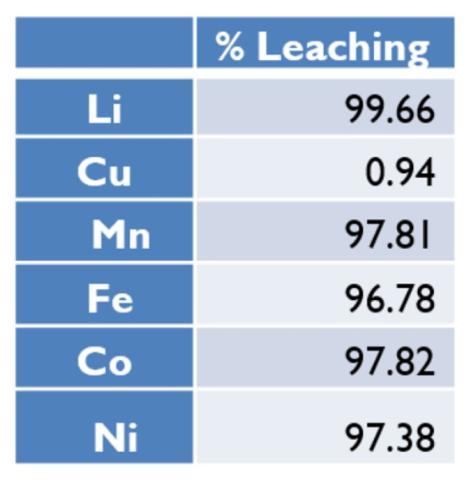