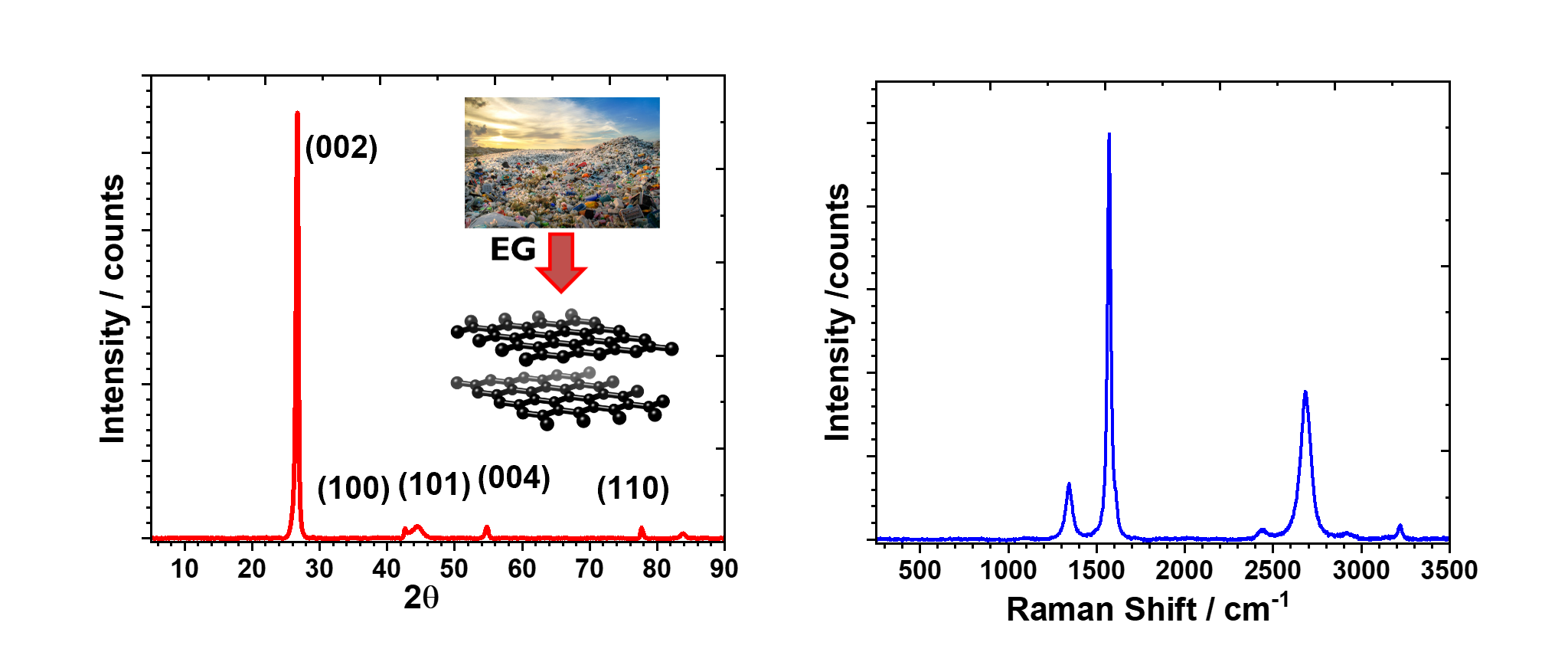
CMI at Oak Ridge National Laboratory, Ames National Laboratory and National Energy Technology Laboratory conducted the activity for this highlight
Innovation
New method of graphitization enables faster graphitization of polyethylene-derived carbonaceous materials at much lower temperature (850 °C) compared to the conventional Acheson process (>3000 °C) and also allows tunability of the graphite structure via active machine learning.
Achievement
Successfully converted waste polyethylene into high quality battery grade graphite, with promising electrochemical performance as an anode for lithium ion batteries.
Significance and Impact
Converting waste plastics to graphite promotes environmental sustainability, reduces pollution, and produces high-quality anode material for lithium ion batteries, supporting electromobility, renewable energy, and circular economy.
Hub Target Addressed
- Recovering critical materials from unconventional sources.
- Developing novel materials processing methods.
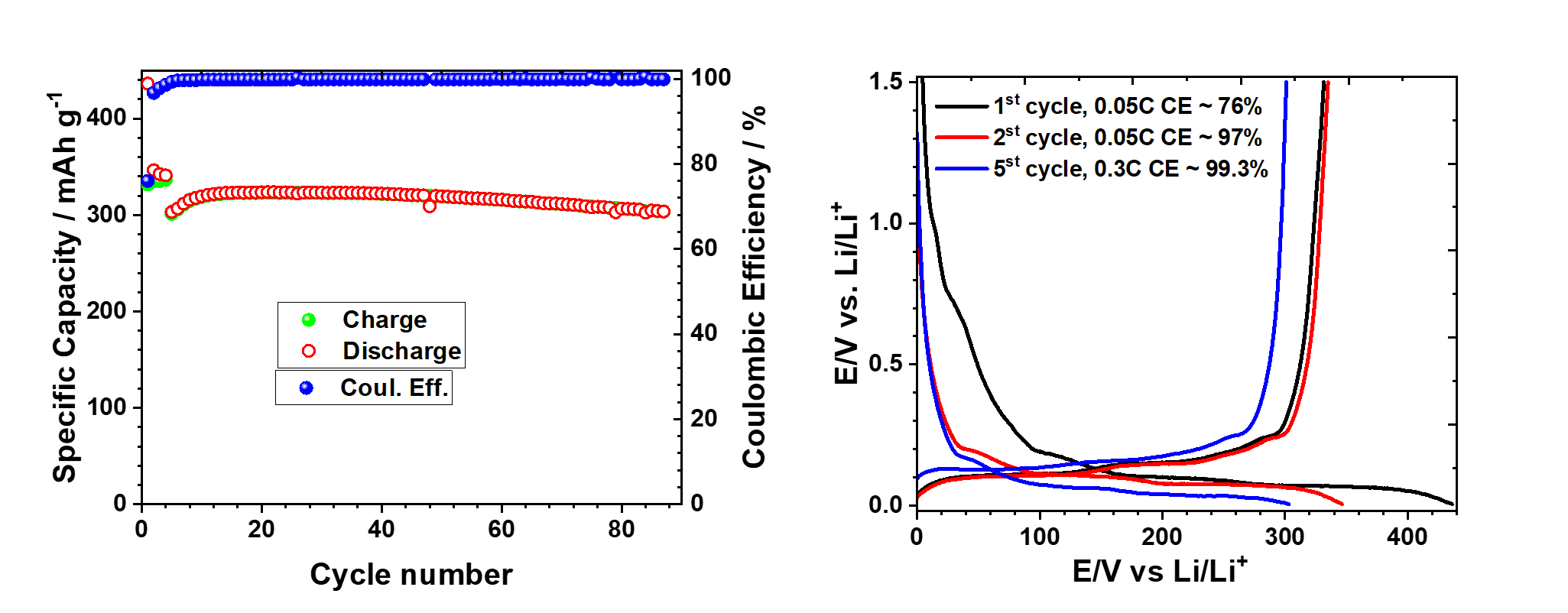