CMI researchers from Lawrence Livermore National Laboratory and Ames National Laboratory conducted the activity for this highlight
Innovation
A high strength additively manufactured Al-Ce alloy aided by computational design was developed and printed using laser powder bed fusion (LPBF) methods.
Achievement
Computational exploration in the hyper-eutectic region of Al-Ce-Mg composition space identified a pathway to avoid the Al13CeMg6 intermetallic phase resulting in an alloy with superior strength and improved microstructure.
Significance and Impact
Rapid solidification rates achieved by LPBF resulted in a nano-composite like microstructure that has superior mechanical properties not only at room temperature but up to 300 °C. The improved microstructural stability contributes to both elevated yield strength (up to 400 MPa) and elongation at fracture of only 7.5%, making this alloy competitive with well established and higher cost additively manufactured Al-Sc alloys.
Hub Target Addressed
Recovering and converting critical materials into high value refined products.
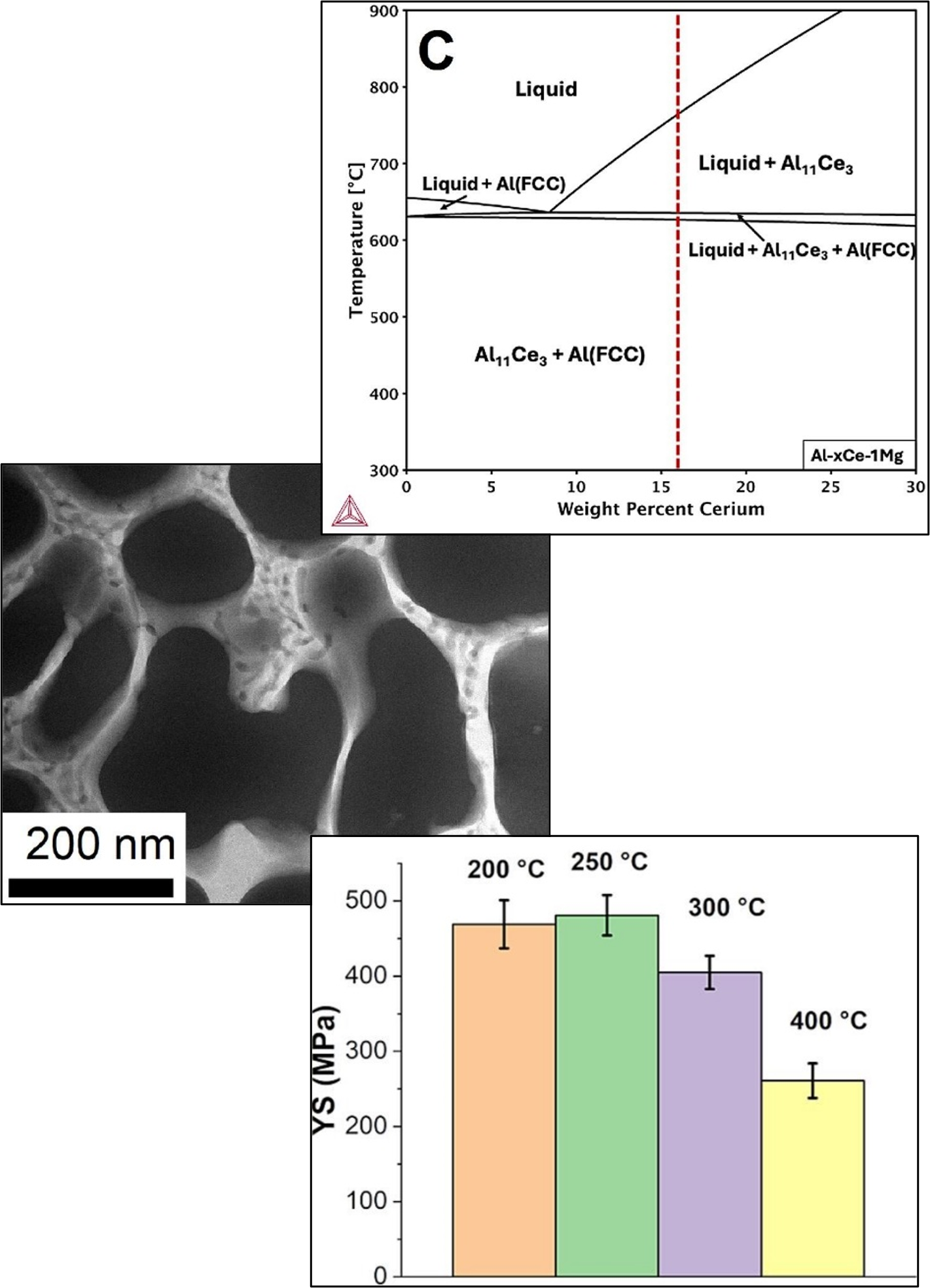