News & Highlights
Bimodal packing NdFeB and SmFeN improves energy product
3D printing of NdFeB bonded magnets with complex shape
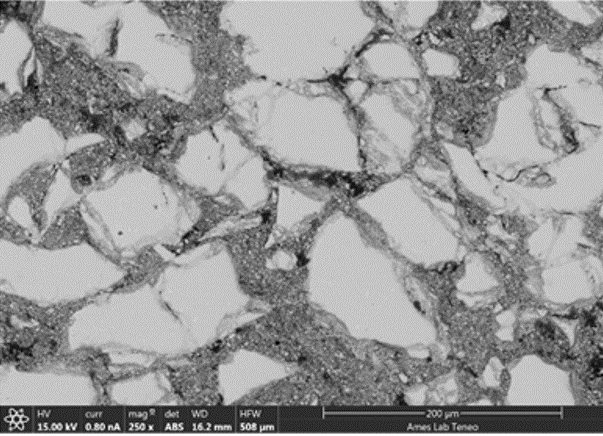
Bimodal packing of NdFeB and SmFeN improves energy product
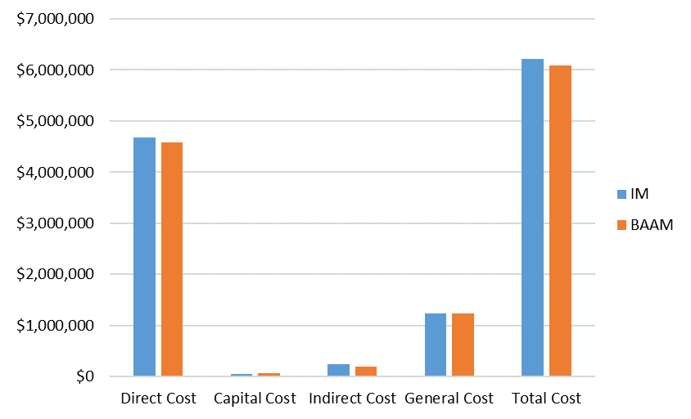
Assessments predict improvements in environmental footprint, profit from printed NdFeB magnets
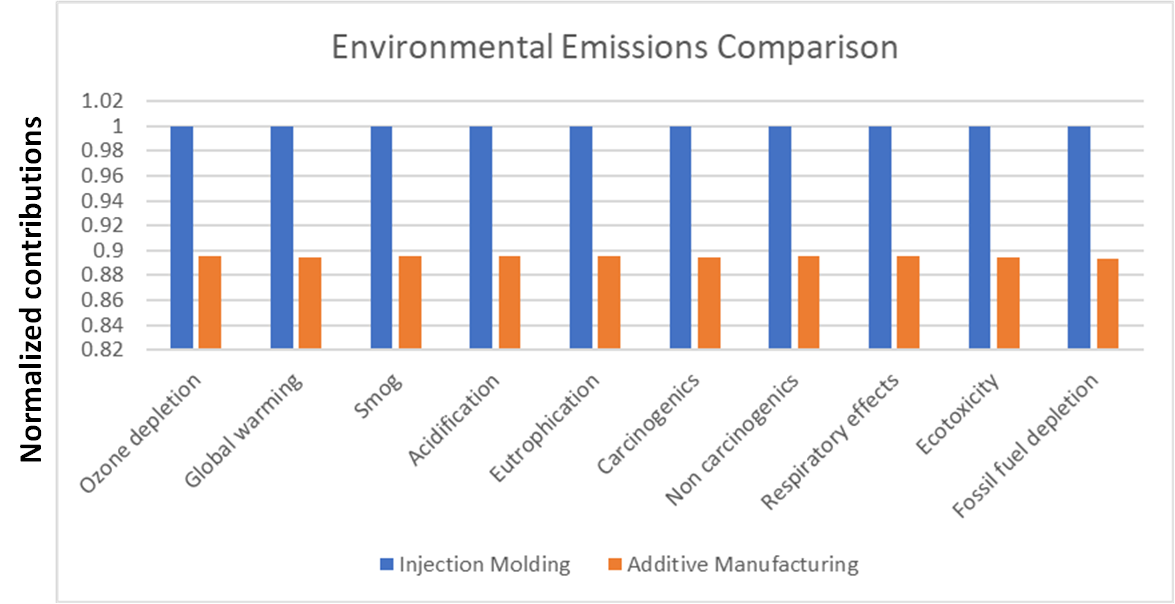
AM magnets enhance performance, reduce environmental impacts
Publications
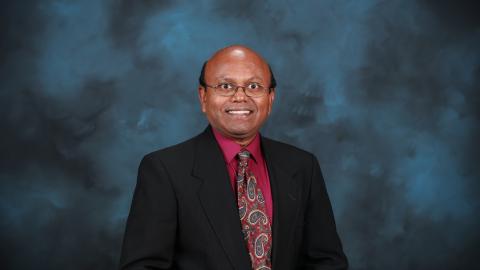
Parans Paranthaman at Oak Ridge National Laboratory leads the CMI project "Additive manufacturing of polymer based bonded magnets"
During sintered rare earth magnet manufacturing, the materials wastage can be up to 48 percent. Additive manufacturing process offer no tooling requirement and almost no wastage. Fabricate near-net shape high-performance magnets with improved corrosion resistance, mechanical properties and thermal stability of up to 150-200 °C, reduce the criticality of Nd, Dy, etc. by minimizing the waste generation associated with magnet manufacturing, and reduce the overall cost. The main goal of this project is to develop gap magnets (with BHmax:20-25 MGOe and beyond) based on anisotropic NdFeB magnets. Printed magnets can offer 30 percent volume reduction and improve motor performance by a factor of two.
Related information:
Research Features LINK
CMI Webinars - several CMI webinars have been offered related to magnets with reduced rare earth content and to this project
R&D 100 Award
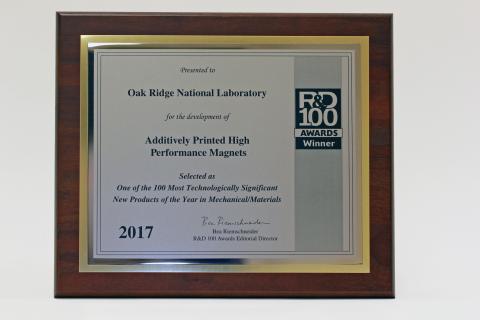
TechConnect Innovation Award
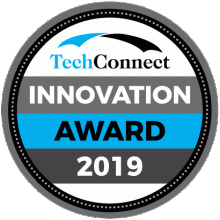