An innovative method of recycling rare earth elements from electronic waste has gone commercial. A team of researchers from the Critical Materials Institute (CMI)
Rare earths are essential ingredients in the magnets that power many technologies people rely on today, such as cell phones, computers, electric vehicles, and wind turbines. Since 1990 supplies of these elements have become limited and recycling them is one way to address their limited availability.
Ikenna Nlebedim, the lead researcher on the recycling project, explained that big companies shred items like
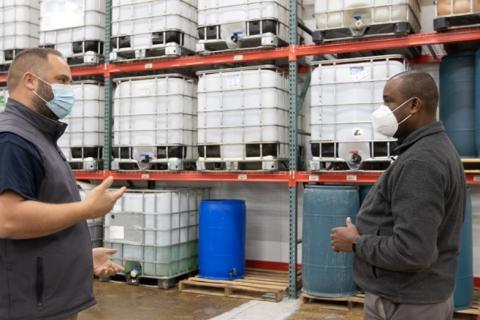
computer hard drives to protect the information on them. Once the drives are shredded, recycling becomes more complex because other recycling methods depend on separating the magnets from other materials. The CMI’s recycling process is designed to extract the rare earths directly from shredded e-waste.
“We take that shredded mix and we put it in solution, but our solution targets the magnet—and it leaves the rest of the components of the mixture undissolved—and dissolves the magnet that contains the rare earths,” said Nlebedim. “So, with the rare earth in solution, we filter off the rest of the e-waste and later pull the rare earth out of the solution. And that's how we do our recycling. It’s a very efficient and robust process.”
This recycling technology has an advantage over other processes because the solution used to dissolve magnets is water-based rather than acid-based. Nlebedim explained that their process begins without acids and the byproducts are treated to eliminate acid-contaminated wastes, which makes it friendlier for the environment.
Other recycling processes involve heating the e-waste to temperatures above 600 degrees Fahrenheit to demagnetize the magnets. The CMI process does not require pre-heating, which leads to reduction in pollution and energy usage.
Denis Prodius, a co-inventor of the technology said, “acid-free dissolution has all the critical features for sustainable recycling. It is environmentally friendly, has demonstrated its economic potential, and efficiently recovers high purity products suitable for commercial applications.”
Since the solution used in this process is copper based, the processed e-waste ends up infused with copper. This copper can be recovered, or it can be reused in other operations. Copper is the key to making the process economically viable and environmentally friendly.
“The dissolution process leaves the other materials in the e-waste intact, making it possible for others to extract materials such as gold and platinum from the leftover materials,” said Kevin Stoll, the engineering project manager of TdVib.
Another important aspect of the technology is its scalability. Upscaling processes from the lab to larger operations often leads to unexpected problems. However, according to Dan Bina, president and CEO of TdVib, upscaling has improved this process.
“It is typical for efficiency to decrease during scaling of new processes, but we have observed the opposite with the acid-free dissolution process, without compromising the purity,” said Bina. “We have increased the leaching efficiency of rare earths from magnets contained in shredded hard drives from around 70% obtained during laboratory research to 90% in our facility. For pre-concentrated magnets the dissolution efficiency can exceed 98%.”
Nlebedim and Prodius have been working on the technology for a few years. Licensing to TdVib LLC is the newest step in its progress from lab to commercialization. The company was initially awarded a Phase I and then Phase II Small Business Technology Transfer (STTR) funding. STTR is a program that encourages small businesses to pursue federal research and development with potential for commercialization.
The goal of Phase II, which is in progress, is to produce three to five tons of rare earth oxide in the next one to two years.
“The technology holds great promise in addressing the limited availability of rare earths for technological applications in the United States,” said CMI Director Thomas Lograsso. “That promise has earned it R&D 100 awards, a Federal Laboratory Consortium award, and a TechConnect Innovation award.”
The CMI is working to create new clean technologies for U.S. industries, like the one involved in this partnership with TdVib.
The Critical Materials Institute is a Department of Energy Innovation Hub led by the U.S. Department of Energy's Ames Laboratory and supported by the Office of Energy Efficiency and Renewable Energy’s Advanced Manufacturing Office, working to decarbonize industry and increase the competitiveness of the U.S. manufacturing and clean energy sectors through process innovations, collaborations, research and development, and technical assistance and workforce training. CMI seeks ways to eliminate and reduce reliance on rare-earth metals and other materials critical to the success of clean energy technologies.
Ames Laboratory is a U.S. Department of Energy Office of Science National Laboratory operated by Iowa State University. Ames Laboratory creates innovative materials, technologies and energy solutions. We use our expertise, unique capabilities and interdisciplinary collaborations to solve global problems.
Ames Laboratory is supported by the Office of Science of the U.S. Department of Energy. The Office of Science is the single largest supporter of basic research in the physical sciences in the United States, and is working to address some of the most pressing challenges of our time. For more information, please visit https://energy.gov/science.