CaloriCool Consortium’s goal: game-changing refrigeration technology within a decade
Refrigeration has been such an integral part of our everyday lives for so long that we rarely think of it. Our food is fresh and our offices and living rooms temperature-controlled thanks to the vapor compression technology developed over a century ago, and it is an integral part of medical care, transportation, military defense, and more.
At Ames Laboratory a new research consortium called CaloriCoolⓇ launched in 2016 with the idea that refrigeration could be radically better—cheaper, cleaner, more precise and energy-efficient—by abandoning vapor compression for something entirely new: a solid-state caloric system. And this research team plans to do it—including adoption into manufactured systems and products—within a decade.
It’s like replacing the incandescent light bulb with an LED bulb; the new technology does the same thing, but in a completely different and much more efficient and sustainable way,” said Vitalij Pecharsky, director of CaloriCool. “That’s what CaloriCool will do with the refrigeration and heat pumping industries.”
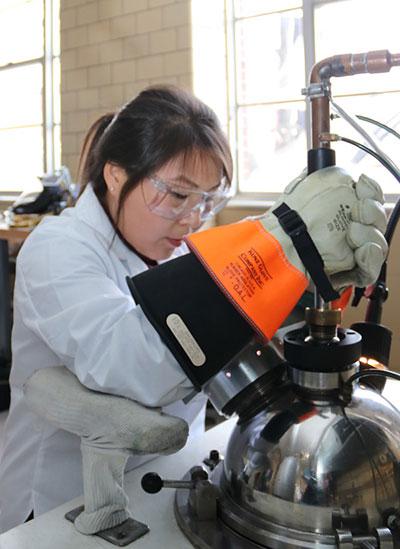
The idea that caloric systems could be used as a replacement for traditional refrigeration technology is actually nothing new. For the last 20 years, materials scientists have been searching for compounds that can generate strong cooling effects when cyclically acted upon by magnetic, electric, or mechanical forces—called magnetocaloric, electrocaloric, and elastocaloric materials. Starting with the discovery of gadolinium-silicon germanium compounds in Ames in 1997, a few other materials are worth mentioning. These include lanthanum-iron-silicon-hydrides and iron-manganese-silicon-phosphides for magnetocalorics, nickel-titanium for electrocalorics, and selected terpolymers for electrocalorics. But none of those materials have been exactly right for commercialization into any kind of product like a residential refrigerator, or building environmental systems.“This is essentially what CaloriCool is going after,” said Pecharsky, who is also an Iowa State University Anson Marston Distinguished Professor of Materials Science and Engineering and Ames Laboratory faculty scientist. “We know the real obstacle preventing the leap into marketable technology is the lack of affordable, high-performance caloric materials.”
The search has already begun in earnest, led by a team of researchers based in Ames and enhanced by partner teams who represent a range of skills vital to the effort, including theoretical analysis, materials design and characterization, engineering design, and technology commercialization. “We’ve already identified several classes of caloric materials that look promising, based on a review of the existing scientific literature, and we are creating samples of them for evaluation,” said Pecharsky.
Experimental work is going forward while the consortium also assembles an informatics system that will be used as both a database and a computational aid tool to assist in evaluating existing and new materials.
“Within five years, we want CaloriCool to be the authority, the resource for information on caloric materials, part of the national materials genome,” Pecharsky said. “That’s going to help accelerate commercialization of the technology.”
Engineering design members of the group have already traveled to Denmark Technical University to establish collaborations and study existing prototype systems for a test station device being designed and built in 2017 called CaloriSMART—Small-scale, Modular Advanced Research Test-station. The test station will allow researchers to rapidly assess whether new materials have the correct properties, can perform as needed for use in a manufactured device, and use the smallest sample necessary to produce reliable data.
“You could read up on how to go about it, but we decided it was better to send our people and let them get their hands on some of these systems, see how they work, and how we can collaborate with experts to build exactly what we need,” said Pecharsky. All of the research in caloric cooling will go hand-in-hand with an analysis of the economic impacts of the technology, including scale-up, technology transfer, and raw materials availability. CaloriCool’s goal is to discover these caloric materials, but they must also be economical, widely available, non-toxic, manufacturable, and create enough energy savings and other benefits that it is attractive to manufacturers and consumers. Early predictions are that caloric cooling systems could result in as much as a 30 percent higher efficiency than currently available vapor-compression products.
“What we are doing is exactly the point of the U.S. Department of Energy’s Energy Materials Network, to really shorten the time frame for materials development to a real, manufactured technology,” said Pecharsky. CaloriCool was one of seven consortia established in 2016 under DOE’s Energy Materials Network and overseen by the Office of Energy Efficiency and Renewable Energy (EERE), specifically to address the need for advanced materials for clean energy technologies. CaloriCool is bringing together national labs, industry, and academia, including Pacific Northwest and Oak Ridge National Laboratories, the University of Maryland, Pennsylvania State University, and Citrine Informatics, all of which have become official partners in 2016.
“The research has been out there a long time; we just needed a new and more aggressive approach to move it from the laboratory to commercialization,” said Pecharsky. “We are quite confident we’ll be able to deliver, and that commercial devices will begin to appear in stores and dealerships near you in five to 10 years.”
EERE's Advanced Manufacturing Office (AMO) supports early-stage applied research and development of new materials, information, and processes that improve American manufacturing’s energy efficiency, as well as platform technologies for manufacturing clean energy products.
Ames Laboratory is a U.S. Department of Energy Office of Science national laboratory operated by Iowa State University. Ames Laboratory creates innovative materials, technologies and energy solutions. We use our expertise, unique capabilities and interdisciplinary collaborations to solve global problems.
DOE’s Office of Science is the single largest supporter of basic research in the physical sciences in the United States, and is working to address some of the most pressing challenges of our time. For more information, please visit science.energy.gov.