Fragile Magnets. Superconductors. Quasicrystals. Materials that are so unusual, unknown, new and puzzling that scientists want to get to know them and their properties better.
Precisely measuring and observing the properties (scientists call this characterization) of new materials requires samples of the purest crystal form of the compound that can be achieved. While there are many methods of producing crystals of new compounds, solution growth is one of the best for discovery and characterization; it is a method that the U.S. Department of Energy’s Ames Laboratory has been pioneering and advancing for 25 years.
That’s the reason one of the Lab’s materials experts, Paul Canfield, a condensed matter physicist, teamed up with LSP Industrial Ceramics, Inc., to build a better piece of lab equipment that now carries his name: Canfield crucible sets.
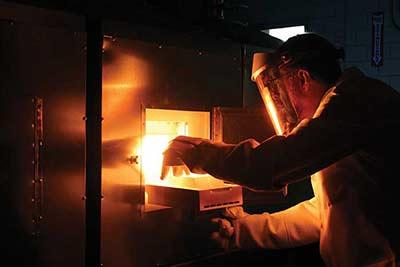
“My primary goal is to advance the science of new materials discovery, and also make it safer and less expensive if I can,” said Canfield, who is also a senior scientist at Ames Laboratory and a Distinguished Professor and the Robert Allen Wright Professor of Physics and Astronomy at Iowa State University.
When compounds have two, three, four or more elements that don’t all solidify at the same temperature, extracting solid crystal compounds out of them can be a challenge; that’s where solution growth comes in. “It’s a very versatile way of growing both known and unknown compounds,” said Canfield. “It’s a good way to access compounds that you cannot readily grow by more conventional techniques.”
Solution growth is similar in concept to the grade school science experiment, growing crystals of sugar or salt from a saturated solution of water. Similar, but not by any means as simple. Solution growth of new compounds in a materials development lab includes high temperature furnaces heated as high as 1,200 C°, thermal gloves, safety visors, centrifuges, and materials which can be toxic or expensive.
The process also requires crucibles— the heat-resistant ceramic containers in which the elements of the desired compound are combined, heated and then cooled to produce a crystal, and spun to separate the newly formed crystal from remaining liquid elements. It was with these small cups and filters that Canfield felt improvements could be made.
In a traditional solution growth experiment, elements are combined in a growth crucible, and topped with a second crucible filled with silica wool, which will act like “a coffee pot with a filter,” said Canfield, straining the liquids from the solids. The entire capsule is then sealed in a glass tube and placed in a furnace for heating and slow cooling. After the temperature is lowered, allowing the desired crystal to form, the assembly is then placed in a centrifuge, which spins any remaining liquid off into the catch crucible with the silica wool separating solid crystals from the remaining liquid metal.
Whereas silica wool has worked well enough over the decades, it has several problems associated with its use as a filter material. (1) It inevitably “sheds” into the growth, leading to either chemical contamination or potential growth sites for unwanted, small crystals. (2) It does not work as a filter for liquids with high surface tension (such as tin near its melting point). (3) After the separation of the remaining liquid from the grown crystals, if any, the solidified liquid is completely mixed and contaminated with the silica wool and cannot be reused or simply analyzed. An additional problem with the use of two crucibles and silica wool was the fact that the two crucibles were not physically attached or secured to each other. This could, in certain cases, lead to leakage of liquid or vapor during growth or separation steps.
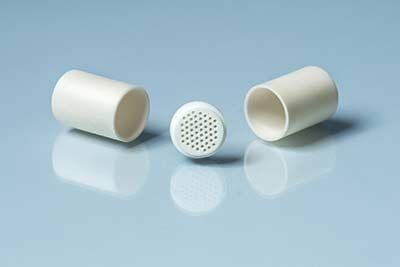
With these concerns in mind, Canfield set about to design a better strainer, a single ceramic disc with holes (called a frit disc) that could be fitted in between the two crucibles. He reached out to LSP Industrial Ceramics, which offers custom-designed lab ceramic supplies.
“Dr. Canfield came up with a design and asked me if it could be made,” said Frank Smith, CEO of LSP Industrial Ceramics. “We made a few changes to make it easier to produce, but it was his plan. We made it come to life.”
While some initial attempts at threading the two crucibles together with the disc were successful, the item was very expensive to make, and the threads made the assembly difficult to take apart after the separation step. Canfield instead settled on a simple design of a step-edged disc between the two crucibles, so that they nestled into each other and, if packed properly into the silica tube, would not misalign or shear apart in the centrifuge.
“Being able to reuse uncontaminated decanted liquid that results from this technique gives us both an economic and scientific advantage,” said Canfield. “It’s less wasteful in terms of the amount of elements we consume, but it also provides additional data points that should help us in terms of being able to refine materials by design.”
Canfield was so pleased with the performance of this new crucible design that he encouraged LSP to offer the crucible sets to other researchers who might want them. “I told Frank if this works, I’m pretty sure all of my friends and colleagues are going to want to use these,” said Canfield. When it came to naming the new item, “I told Frank that if Erlenmeyer could have his flasks, then Canfield could have his crucibles.” And so the Canfield Crucible Set was born.
Smith said the eventual worth to other customers evolved on its own, partly through enthusiastic word-of-mouth reviews from colleagues and graduate students who had worked with Canfield. Or from Canfield himself, who likes to hand them out at conferences and seminars, and has published papers on the performance of the crucibles.
“The feedback has been beyond positive, and we have dozens of laboratories, from highly respected universities and research facilities to government agencies utilizing these parts. Our collaboration with Ames Laboratory has been very successful,” said Smith.