The Critical Materials Institute (CMI) is a DOE Energy Innovation Hub lead by Ames National Laboratory, with the mission to accelerate the development of innovative scientific and technological solutions. CMI researchers at national laboratories and industry developed a technology to help separate rare earth elements. This technology is licensed to Marshallton Research Laboratories, which was founded more than 40 years ago. As this CMI project draws to a close, Marshallton is excited about opportunities for what comes next.
Marshallton, based in King, North Carolina, worked with researchers at Oak Ridge National Laboratory and Idaho National Laboratory to develop new chemistries that can enable domestic production of rare earth elements by providing economically viable and environmentally sustainable alternatives for REE separations using novel separation technologies that significantly reduce capital and operating costs.
“Finding good ways to separate elements from each other is something that we’ve been good at, but we can always do better,” says Marshallton’s Mac Foster, who joined the company in 1989. “Rare earth separations has been identified as a grand challenge problem.”
CMI has worked to identify and address Grand Challenge Problems, which include how to separate rare earth elements from each other LINK.
“Working within the framework of CMI, we collaborated with ORNL and INL to identify new candidates that are effective, both for separations and for cost,” Foster explains. The group met this goal with new extraction agents based on diglycolamides, or DGAs. One that they developed and tested is known as DGA-6, which was licensed to Marshallton in 2021 LINK.
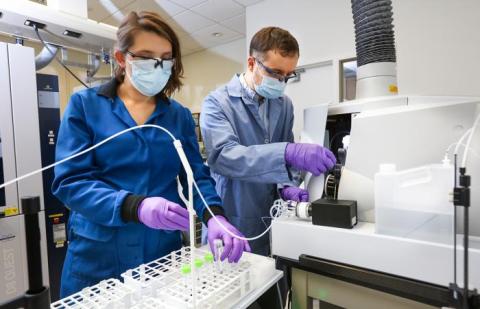
Now, Marshallton is working to meet increasing need for DGA-6 from a variety of companies.
“We’re working with several companies while also improving and scaling up manufacturing processes,” Foster explains. “The idea is to be prepared for increasing demand in industry now that we have demonstrated a process flowsheet that can scale to the multi-ton per year level.”
Foster says the process improvement continues, too. “Improvement is never finished,” he says. “There’s always room for improvement. We see a pathway to make improvements to meet the growing demand.”
While most of the companies Marshallton is working with are affiliates of CMI, Foster says some aren’t – at least not yet. “When supplying to private companies, if they aren’t already a CMI Affiliate, then I encourage them to join the CMI family,” he says.
CMI is a public-private consortium, with a network of 100 partners across critical material supply chains. This includes CMI Team members, including Marshallton, that collaborate on research to develop new technologies. It also includes CMI Affiliates, which are interested in the technologies and processes.
In the search for new technologies needed to develop resilient and secure supply chains for rare earth metals and other materials critical to the success of clean energy technologies, CMI has developed capabilities in computational ligand design, synthesis, process modeling, and flowsheet testing that are well poised to address the Hub’s strategies for source diversification by eliminating economic and technological bottlenecks in the supply chain for critical materials.
Separation of individual rare earth elements (REE) is regarded as the most difficult processing step in the production of high purity rare earth oxides for end-use technology applications due to their inherent chemical similarities.