The Critical Materials Innovation Hub (CMI Hub) worked with industry to take a key step in how to process rare earth metals in the United States. The capability to produce these metals is needed to create a U.S. supply chain for neodymium iron boron permanent magnets. Such magnets are used in electric vehicle traction motors and offshore wind turbine generators. CMI Hub Open Innovation Projects (OIP) brought together industry, universities and national laboratories. This project included Terves LLC, Worcester Polytechnic Institute (WPI), Ames National Laboratory and Powdermet Inc. For two years, they worked on how to produce and refine rare earth metals.
“OIP projects are led by industry to help the next generation of CMI Hub research and development align with industry needs. This project helps enable a domestic supply of rare earth metals for strong permanent magnets,” says CMI Hub Director Thomas Lograsso, Ames National Laboratory. “These metals are used in multiple industries. They had relied on midstream processing overseas. Through this work, we made ways to bring that to the United States.”
Andrew Sherman, Terves Chief Executive Officer, served as project lead. The research group started in spring 2021. Their two-year goal focused on using heat and metal to make high purity neodymium. The key was creating low temperature, scalable processes using the Terves foundry to speed up establishing rare earth metal manufacturing in the United States. The collaboration between industry, university and national laboratory met their goals for making rare earth metal.
Terves worked with the Materials Preparation Center (MPC) at Ames National Laboratory on purification. MPC is a specialized research center recognized for its unique capabilities in purification, preparation and characterization of rare earths, metals, alloys, and single crystals.
Matt Besser, MPC director, says capabilities within the MPC were repurposed. High-purity calcium metal usually is added to rare earth fluorides to reduce into rare earth metals. High-purity calcium is made by MPC using vacuum distillation where calcium is vaporized and collected, leaving behind impurities that are detrimental in reduction processing. Here, they used the same process to separate volatiles like magnesium and calcium from neodymium from the rare earth metal that was reduced by Terves. “The desired metals are left behind and the rest can be reused in the process,” Besser said. “We used arc melting to remove other unwanted bits. This left us with pure rare earth metals.”
Sherman notes the team success meets the goal to refine neodymium at a small scale and increase to pilot scale. They worked with MPC to produce high purity neodymium. And, they showed how to make a new metal from recycled raw materials for making magnets. This made a mixed metal of neodymium, praseodymium and dysprosium, which theoretically can be used directly in the production of neodymium iron boron permanent magnets.
WPI made models that helped refine the process. The Terves team used the models to refine metal and salt compositions at lower processing temperatures. This paves the way to use less energy and lower the cost of supplies. The team also worked with Purdue University who developed a techno-economic analysis and a pricing model.
This work has generated intellectual property, know-how and enhanced capabilities at Terves. The company has plans to continue work through other funding. “Overall, these collaborations included a lot of support from the Laboratory,” Sherman says. “Transferring know-how to industry is a great collaboration model.”
In 10 years of work, 20 CMI Hub technologies have been licensed. The CMI Hub has 585 publications and 47 patents. The CMI Hub has developed six open-source software packages. To partner with the CMI Hub or license CMI Hub technologies, contact Stacy Joiner, CMI Partner Relations, sjoiner@ameslab.gov or 515-296-4508.
The Critical Materials Innovation Hub (CMI Hub) is a Department of Energy Innovation Hub led by the U.S. Department of Energy’s Ames National Laboratory and supported by the Office of Energy Efficiency and Renewable Energy’s Advanced Materials and Manufacturing Technologies Office (AMMTO). The CMI Hub seeks ways to accelerate the development of critical material technologies and enhance the innovation pipeline for U.S. supply chains by accelerating research, educating a diverse workforce, and creating de-risked, commercial-ready technologies in partnership with American industry.
Ames National Laboratory is a U.S. Department of Energy Office of Science National Laboratory operated by Iowa State University. Ames Laboratory creates innovative materials, technologies and energy solutions. The Office of Science is the single largest supporter of basic research in the physical sciences in the United States, and is working to address some of the most pressing challenges of our time. For more information, please visit https://energy.gov/science.
###
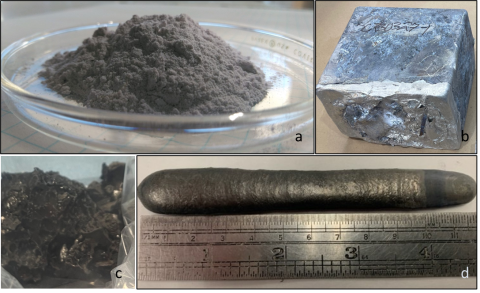