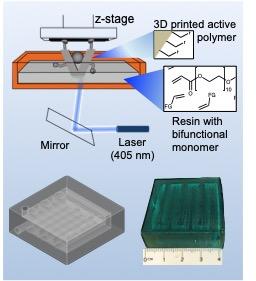
There has been large interest in the application of additive manufacturing to several technological and scientific fields. Despite the significant developments in medicine, physics and engineering, little has been explored on the potential applications of this new technology to chemical sciences. One possible set of applications includes controlling the performance of heterogeneous catalysts by manipulating the flow of reactants through beds with complex topologies that maximize reactant-catalyst collisions without decreasing space velocity. To explore ideal reactor topologies one could take advantage of 3D printing, however application of catalysts to complex 3D structures via traditional methods such as washcoating are unlikely to provide homogeneous site distributions and would therefore be unable to provide any benefit compared to traditional honeycomb structures.
To circumvent this limitation we developed an approach that produces catalytically active materials directly during 3D printing, thus ensuring homogeneous distribution and high concentration of active sites in any target 3D structure. In this approach a substituted olefin is used as the building block for the 3D material. Photopolymerization of the olefins via stereolithography allows formation of the target architectures, while the substituent in the original molecule carries the catalytically active moiety. The substituent can be selected from a large number of known chemical catalysts, providing a versatile approach to control the chemistry and the macroscale architecture of catalysts. We demonstrated the direct printing of acid, bifunctional and cooperative acid-base, and metallic catalysts and their application to 3 different test reactions. We also demonstrated the application of the method to produce unique tools such as a catalytic UV cuvette adaptor that allows monitoring the kinetics of heterogeneous catalytic reactions in situ using inexpensive equipment, or millifluidic devices whose catalytic performance depends on channel morphology.
Manzano, J.S.; Weinstein, Z.; Sadow, A.D.; Slowing, I.I., Direct 3D Printing of Catalytically Active Structures, ACS Catal, 2017, 7, 7567-7577.